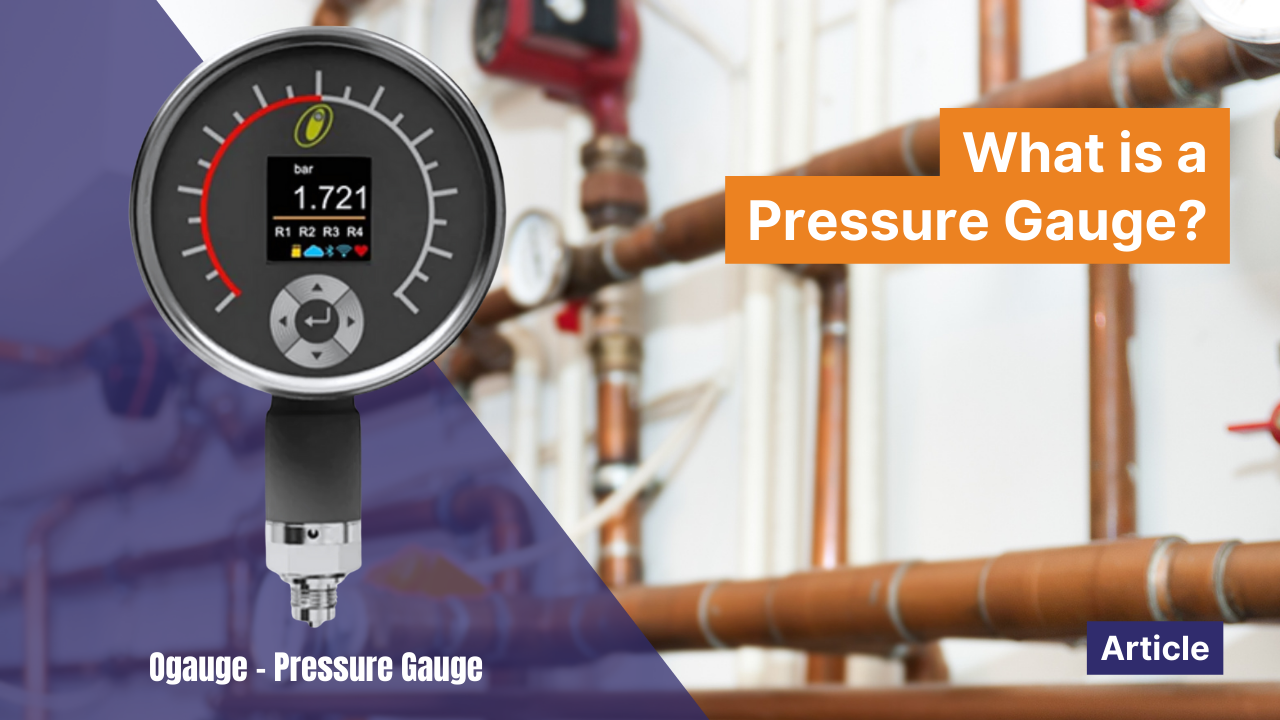
Understanding Pressure Gauges: Essential Tools in Industrial Applications
Pressure gauges are indispensable tools in industrial settings, serving as critical instruments for measuring the internal pressure of media within various systems. Their role is as fundamental as temperature measurement, essential for ensuring product quality and facility safety. Pressure gauges enable monitoring and control of pressure, making industrial processes predictable and reliable.
Without pressure gauges, fluid power machines designed to operate within specific pressure ranges would face unpredictable failures. Properly installed pressure gauges help industry professionals troubleshoot and address leaks or unwanted pressure changes, ensuring smooth and safe operations.
Types of Pressure Gauges and Their Functionality
Understanding the different types of pressure gauges and their functionalities is crucial for selecting the correct gauge for specific applications. The term "pressure gauge" often overlaps with terms like sensor, transducer, and transmitter. However, a pressure gauge typically refers to a self-contained indicator converting detected process pressure into the mechanical motion of a pointer.
1. Mechanical Pressure Gauges
Mechanical pressure gauges were the first to use flexible elements as sensors. These gauges employ a Bourdon tube, diaphragm, or bellows element that detects process pressure and moves accordingly. This motion translates to the rotation of a pointer in front of a dial, providing a visual representation of the pressure level.
2. Analogue Pressure Gauges
Analogue pressure gauges have been industrial mainstays for over a century. They use a needle to indicate pressure on a dial scale, are inexpensive, easy to use, and require no power source. However, they are prone to damage and inaccuracies due to mechanical vibrations or harsh conditions, necessitating consistent maintenance or regular replacement.
3. Bourdon Tube Gauges
Bourdon tube gauges operate on the principle that a curved tube straightens under pressure. This tube is connected to a pointer, which moves along a calibrated dial to indicate pressure fluctuations. Bourdon tube gauges are highly effective for medium to very high pressures applications.
4. Diaphragm and Bellows Gauges
Diaphragm and bellows gauges use an elastic element that expands and contracts in response to pressure changes. These gauges are ideal for measuring lower pressure ranges where Bourdon tube gauges are less effective. The internal bellows connected to a pointer ensure accurate dial pressure readings.
Digital Pressure Gauges: The Modern Solution
Digital pressure gauges have gained popularity due to their high accuracy, durability, and clear readability. Unlike their analogue counterparts, digital gauges perform well under extreme conditions and maintain calibration over extended periods. They provide precise measurements and additional data for analysis, enhancing control and monitoring capabilities.
Advantages of Digital Pressure Gauges
Digital pressure gauges offer several advantages over analogue gauges. They can handle heavy mechanical vibrations, stay calibrated longer, and provide precise readings for very low pressures or small incremental changes. These gauges can also send data to computers, data loggers, and other instruments, facilitating comprehensive analysis.
Advanced Features of Digital Gauges
Digital pressure gauges come with various advanced features, including changing units, recording minimum and maximum data, and integrating backlights and alarms. These features enhance their functionality, making them suitable for complex industrial applications requiring detailed pressure monitoring and control.
Specialised Pressure Measurement Techniques
Different industrial applications require specific types of pressure measurement techniques. Understanding these techniques helps in selecting the appropriate gauge for accurate readings and efficient operations.
1. Strain Gauge
Strain gauges measure pressure by detecting deformation in a diaphragm connected to a strain gauge. This deformation changes the gauge's resistance, producing a variation in output voltage proportional to the pressure. Strain gauges are effective for applications requiring precise pressure measurements.
2. Piezoelectric Gauges
Piezoelectric gauges utilise crystals that generate an electrical charge when strained. The stress on the diaphragm produces a strain that converts to an electric charge, proportional to the pressure. Piezoelectric gauges are known for their high sensitivity and accuracy in pressure measurement.
Selecting the Right Pressure Gauge
Choosing the right pressure gauge involves understanding different types of pressure and their reference points. Pressure measurement is categorised into gauge pressure, absolute pressure, differential pressure, and compound pressure, each serving distinct industrial needs.
Types of Pressure
- Gauge Pressure (psig): Measured in relation to local ambient pressure, it includes the pressure from atmospheric weight and varies with altitude and weather conditions.
- Absolute Pressure: Measured relative to a perfect vacuum, providing a true measure of the internal pressure.
- Differential Pressure (psid): Measures the pressure difference between two points, useful in applications requiring precise monitoring of pressure variations.
- Compound Gauge Pressure: Measures both positive and negative (vacuum) pressures, suitable for systems experiencing a range of pressure conditions.
Conclusion
Pressure gauges are vital instruments in industrial operations, ensuring product quality and facility safety through accurate pressure measurement and control. Understanding the types, functionalities, and applications of pressure gauges helps in selecting the right tool for specific industrial needs. Whether opting for traditional analogue gauges or modern digital ones, the right pressure gauge enhances operational efficiency and reliability.